Striving for Zero-Waste: Ways to Change Your Design Approach
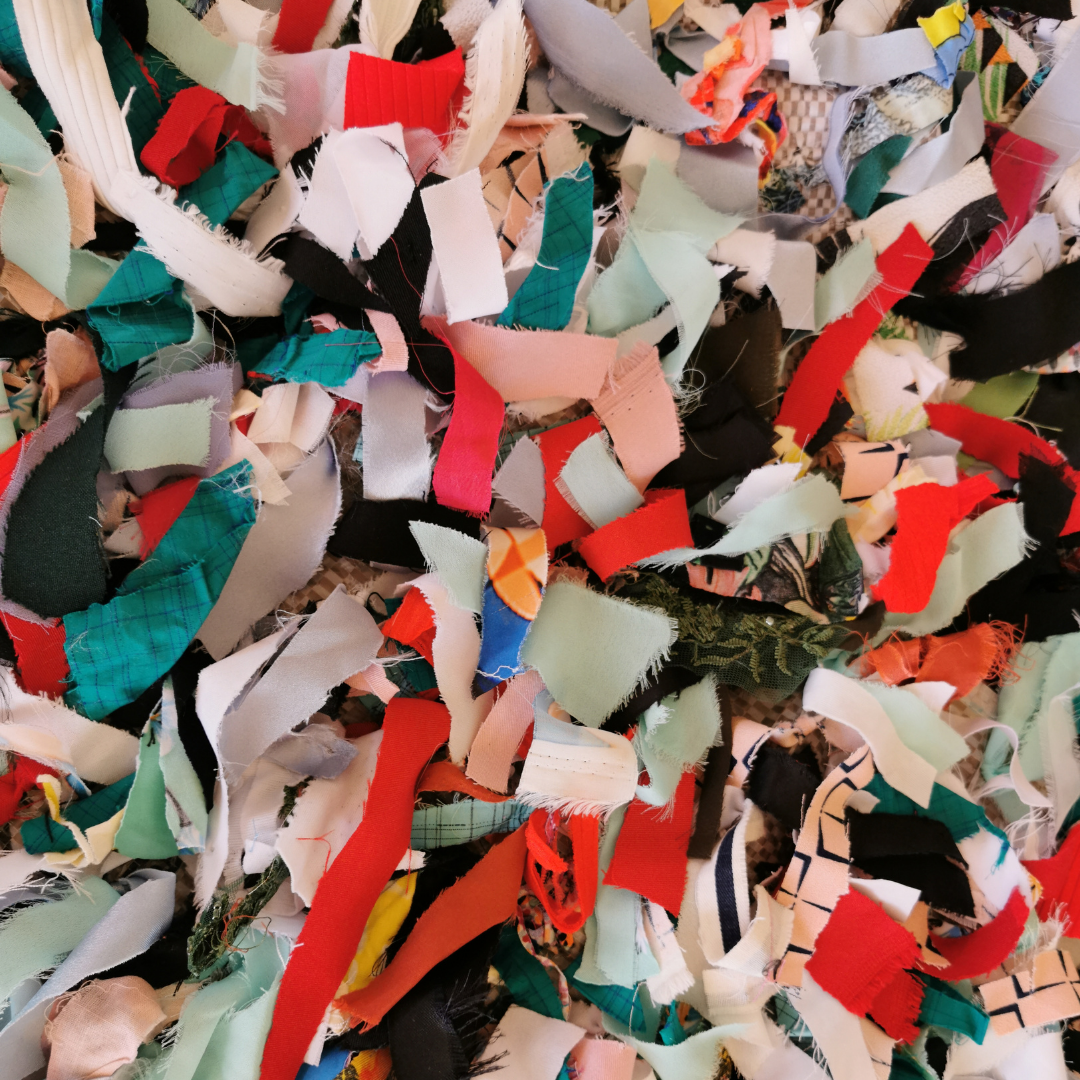
The fashion industry is contributing to the environmental and social crises on an ever increasing scale. The industry is responsible for the production of 92 billion tons of waste every year and the figure is growing significantly as consumption is also increasing. It’s been estimated that 15% - 25% of textile intended for clothing ends up on the cutting room floor. Not only this is a waste of the natural resources used to produce these textiles, but also of the human labour went into creating the fabric.
However, waste is often treated as a management problem, not as a design flaw. From textile scraps, leftover fabric, to excess thread, there’s a whole lot that needs to be reduced, reused and recycled from the manufacturing process.
In the fashion industry, the progress toward zero-waste design and developing more sustainable forms of manufacturing is still slow. Designers and brands must integrate sustainability by exploring sustainable design solutions such as design concept, material choices, pattern development, assembly practices and product life cycle.
What is Zero-Waste Design?
Zero-waste fashion design is concerned with reducing or ideally eliminating textile waste in the production of garments. While eliminating 100% of waste is not always possible and a small percentage may be left, it is always the goal to create no waste. Any additional leftovers can be used for functional items such as scrunchies, face masks or detail such as appliqués and pockets.
The zero-waste approach towards designing and constructing garments is not entirely a new concept. Many historical clothing items consciously designed patterns and concepts wherein less fabric was wasted in the process of contracting fashionable garments.
From whole garment knitting, zero-waste pattern cutting and Direct Panel on Loom, there is several techniques, strategies, alternative processes and approaches that can be taken to design garments that create a low environmental impact and positive social purpose.
Zero-Waste Pattern Cutting
Zero-waste design technique eliminates textile waste at the design stage. Working with zero-waste patterns can be tricky. This technique requires careful planning on how a piece of textile is used by arranging the pattern pieces like a jigsaw puzzle. Garments design is influenced by the pattern cutting process itself rather than the conventional sketch. Therefore, the primary design consideration is the pattern cutting. Dropping is one of the common techniques that can help working out the pattern.
Similarly, Subtraction Cutting is another innovative technique. The resulting shape is created by the removal of fabric, rather than the addition of fabric. This removal creates empty space for the body to occupy but also affects how the fabric drapes around the body. The basic premise of Subtraction Cutting is that the patterns cut do not represent garments outward shape, but rather the negative spaces within the garment that makes them hallow.
While incorporating one of these techniques, dead stock fabrics (fabrics that is leftover from mills and factories, or flawed fabrics) or other unused materials that otherwise end up in a landfill. By reusing materials that already exist, you are saving energy, water, chemicals and other resources required to make new virgin materials. Every tonne of discarded textiles that is reused stops 20 tonnes of CO2 from entering the atmosphere.
Whole Garment Knitting / 3D Knitting
Usually, knitwear is produced by knitting each part (from body, back body, and sleeves, etc) separately, and sewing them together. Whole garment knitting produces the knitwear in one entire piece three-dimensionally, preventing waste material such as cut loss and seam allowance. As a garment is made directly from yarn, the fabric manufacturing process is eliminated, and no waste will be generated.
Using 3D knitting machine that creates items from one yarn prevents overproduction and textile waste, and creates less than 1% of unused material. Both techniques can also allow the garment to have greater freedom of movement and increase comfort for the wearer.
Direct Panel on Loom (DPOL)
DPOL method creates a garment by weaving fabric in the shape of garment panels (pieces). This method uses a computer attached loom that helps weaving made to measure garment section. The segmented pieces of a garment are sewn together by hand. It decreases the usage of yarn, dyes, chemicals and reduces lead time by 50%, and saves 70 to 80% of water in comparison to other garment manufacturing methods used commercially.
Reducing waste in the fashion industry requires a holistic transformation of the internal design and management processes of the industry. Technologies like 3D knitting and techniques like zero-waste pattern cutting will pave way for sustainable fashion. It’s important to note that, reducing waste will only have a minor positive effect on the environmental outcomes only if we reduce consumption of raw materials.
Currently, most techniques above cannot be implemented in large manufacturing units due to the added expense of training labour and changing the dynamics of a traditional pattern making set-up. With the growing demand for sustainability initiatives, the concept of zero waste design needs to progress from individual designers to mass markets and towards commercialization to change the way textiles are being used and create positive environmental impact.
Dhakai wants to know: In what ways could you change your design process to reduce production waste?